Plastic extrusion for intricate profiles and custom designs
Plastic extrusion for intricate profiles and custom designs
Blog Article
A Comprehensive Overview to the Process and Advantages of Plastic Extrusion
In the huge realm of manufacturing, plastic extrusion emerges as a essential and extremely reliable procedure. Translating raw plastic right into continuous profiles, it caters to a wide variety of sectors with its exceptional versatility.
Understanding the Fundamentals of Plastic Extrusion
While it may show up complicated at initial glance, the procedure of plastic extrusion is essentially straightforward. The procedure starts with the feeding of plastic product, in the type of pellets, powders, or granules, right into a warmed barrel. The designed plastic is after that cooled, solidified, and cut into desired sizes, completing the procedure.
The Technical Process of Plastic Extrusion Explained

Sorts Of Plastic Suitable for Extrusion
The option of the best sort of plastic is a critical aspect of the extrusion process. Various plastics use unique homes, making them extra matched to specific applications. Polyethylene, as an example, is commonly utilized as a result of its inexpensive and easy formability. It supplies superb resistance to chemicals and moisture, making it suitable for items like tubes and containers. Similarly, polypropylene is one more prominent choice due to its high melting factor and resistance to fatigue. For even more durable applications, polystyrene and PVC (polyvinyl chloride) are typically selected for their stamina and resilience. These are common options, the selection inevitably depends on the specific requirements of the item being generated. So, comprehending these plastic types can considerably enhance the extrusion procedure.
Contrasting Plastic Extrusion to Other Plastic Forming Methods
Comprehending the types of plastic appropriate for extrusion paves the means for a wider conversation on exactly how plastic extrusion piles up against other plastic forming approaches. Plastic extrusion is unequaled when it comes to producing constant accounts, such as pipelines, gaskets, and seals. It also allows for a constant cross-section along the length of the item.
Key Advantages of Plastic Extrusion in Production
In the realm of production, plastic extrusion offers several significant advantages. One remarkable advantage is the cost-effectiveness of the procedure, that makes it a financially attractive manufacturing approach. In addition, this technique provides exceptional product flexibility and improved manufacturing rate, thereby enhancing overall production efficiency.
Economical Production Method
Plastic extrusion leaps to the forefront as an economical manufacturing method in production. This process stands out for its capability to produce high quantities of product promptly and successfully, offering producers with significant cost savings. The main expense benefit is the capability to make use of cheaper resources. Extrusion makes use of polycarbonate materials, which are much less expensive compared to metals or porcelains. Better, the extrusion process itself see post is reasonably straightforward, reducing labor costs. Additionally, plastic extrusion needs less power than conventional manufacturing methods, adding to reduced operational prices. The process additionally reduces waste, as any type of faulty or excess materials can be recycled and reused, giving an additional layer of cost-effectiveness. Generally, the financial benefits make plastic extrusion a highly eye-catching option in the production sector.
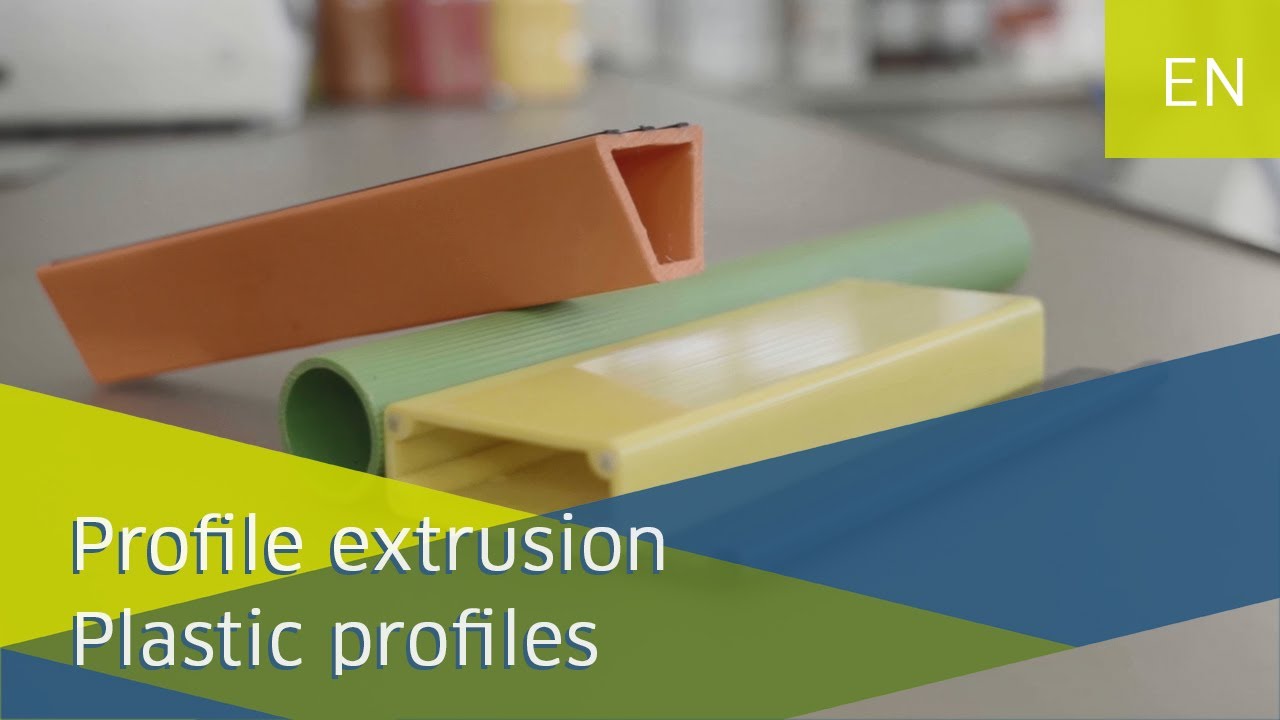
Superior Product Versatility
Beyond the cost-effectiveness of plastic extrusion, one more significant advantage in manufacturing lies in its remarkable item flexibility. This makes plastic extrusion an excellent remedy for sectors that need customized plastic elements, such as automotive, building and construction, and packaging. In essence, plastic extrusion's product flexibility fosters technology while improving functional effectiveness.
Improved Production Rate
A substantial advantage of plastic extrusion exists in its boosted you could check here production rate. Few various other manufacturing procedures can match the rate of plastic extrusion. Additionally, the ability to maintain constant high-speed manufacturing without giving up product top quality establishes plastic extrusion apart from various other approaches.
Real-world Applications and Impacts of Plastic Extrusion
In the realm of manufacturing, the strategy of plastic extrusion holds extensive significance. look at this website The economic benefit of plastic extrusion, mostly its cost-efficient and high-volume outcome, has transformed manufacturing. The sector is constantly aiming for technologies in recyclable and biodegradable materials, indicating a future where the benefits of plastic extrusion can be retained without compromising environmental sustainability.
Final thought
In conclusion, plastic extrusion is a very reliable and efficient approach of changing resources into diverse items. It supplies countless advantages over various other plastic developing techniques, including cost-effectiveness, high output, marginal waste, and layout versatility. Its influence is profoundly felt in numerous industries such as construction, automobile, and durable goods, making it a critical procedure in today's manufacturing landscape.
Delving much deeper into the technical procedure of plastic extrusion, it starts with the choice of the proper plastic material. When cooled, the plastic is cut right into the needed sizes or injury onto reels if the item is a plastic movie or sheet - plastic extrusion. Contrasting Plastic Extrusion to Other Plastic Forming Methods
Comprehending the types of plastic ideal for extrusion leads the means for a wider discussion on just how plastic extrusion stacks up versus other plastic forming methods. Couple of other production processes can match the speed of plastic extrusion.
Report this page